Aluminum Gantry Cranes
Material handling systems, such as our adjustable Aluminum Gantry Cranes, are essential to reducing accidents and improving your company’s overall efficiency. Our systems meet Occupational Safety and Health Administration (OSHA) and American National Standards Institute (ANSI) standards, so you can use our products to help protect your materials and employees.
Explore our Aluminum Gantry Cranes below to see how Spanco can benefit your facility.
- Capacities: up to 3 tons
- Adjustable Height Under I-beam: up to 12’ 4″
- Adjustable Spans: up to 20’ on 1-ton models and 15′ on 2 and 3-ton models
Starting as light as 116 pounds, Spanco Aluminum Gantry Cranes are lightweight, portable, and extremely stable under load.
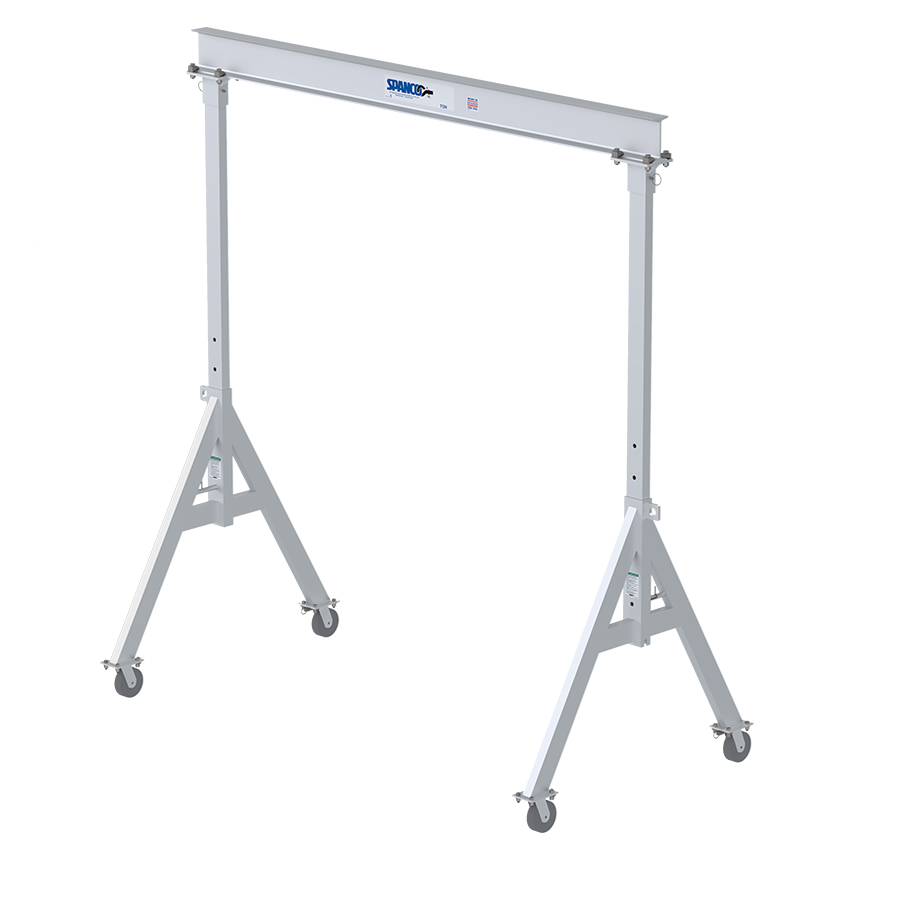
Options & Components
Need a System Fast?
Learn about our Fast-Track Offering
Find Out More
Additional Information
These Spanco All-Aluminum Gantries quickly assemble and disassemble, making them popular with contractors who need highly mobile lift equipment that they can take in their service trucks.
Just one or two workers can typically move a disassembled crane up stairways, onto roofs, or in other challenging locations. When on location, the gantry cranes are rapidly assembled, ready to lift, and able to position heavy objects precisely, such as bulky HVAC units.
Because they are corrosion resistant, aluminum gantries are also ideal for refrigerated areas and other controlled environments, making them increasingly popular with HVAC contractors.
FEATURES OF SPANCO ALUMINUM GANTRY CRANES
- Crane Height Adjustments: Adjusting in 6-inch increments, height adjustment kits use spring-loaded steel locking pins that automatically engage when height positioning holes are reached; adjust heights for specific lifts, uneven floors, or to move through doorways.
- Adjustable Spans: Standard on aluminum cranes, adjustable spans are optional on steel cranes; adjustable spans allow the crane to be shortened for transport down narrow aisles.
- Heavy-Duty Casters: Four-position, swivel-lock casters with moldon polyurethane wheels provide excellent floor protection.
Common Product Uses
At Spanco, we are proud to serve customers in diverse industries. The Spanco A-Series Aluminum Gantry Crane is one of the most versatile models we produce and has some of the most unique applications of all Spanco systems. Some of the many ways customers have used our portable gantry cranes include:
- The Metropolitan Museum of Art (MET): To preserve and document an extensive collection of Islamic rugs, the Metropolitan Museum of Art needed a lightweight material handling system that could assist with photographing detailed sections. They purchased a Spanco Aluminum Gantry Crane, which allowed them to create a digital archive while preserving the rugs’ integrity.
- HVAC company: An Indiana-based HVAC company needed a material lifting solution that could be used at multiple job sites for commercial and residential clients. Multiple one and two-ton Spanco Aluminum Gantry Cranes provided lightweight and portable solution they needed to move air conditioners and other heavy HVAC units on the job.
- Automotive Garage: Since Extreme Performance and Off-Road is a custom car garage, its mechanics often remove or replace engines with a two-ton engine hoist. A Spanco Aluminum Gantry Crane allowed the team to improve efficiency for a variety of tasks and provide higher-quality services.
- Compressed Air Company Uses Spanco Aluminum Gantry Crane for Field Operations
- Industrial Fabrication Contractor Uses Workstation Bridge Crane and Aluminum Gantry Crane to Streamline Manufacturing Process
- Metropolitan Museum Uses Custom Aluminum Gantry to Create A Digital Archive & Preserve Ancient Islamic Art
- Aluminum Gantry Crane Improves Workflow at Custom Car Garage
- Aluminum Gantry Cranes Improve Efficiency for HVAC Company
Spanco, Inc. warrants its products to be free from defects in material and workmanship as follows:
- Manual Systems & Equipment: Ten Years
- Motorized Systems & Equipment: One Year
- Paint & Finishes for Non-Aluminum Components: Two Years
Ten-Year Warranty Coverage:
- Defects in equipment material and workmanship of manual systems and equipment
- Wearable parts (workstation bridge crane end trucks and hoist trolley wheels only)
Spanco, Inc. warrants its manual workstation bridge crane, jib crane, and gantry crane products to be free from defects in material and workmanship for a period of ten (10) years or 20,000 hours, commencing on the date of shipment to the first retail purchaser. This warranty extends to non-wearable parts only, with the exception of the wheels supplied on manually operated workstation end trucks and hoist trolleys.
One-Year Warranty Coverage:
- Defects in equipment material and workmanship of motorized systems and equipment
Spanco, Inc. warrants motorized equipment to be free from defects in material and workmanship for a period of one (1) year or 2,000 hours, commencing on the date of shipment to the first retail purchaser.
Two-Year Warranty Coverage:
- Paint coatings and finishes for non-aluminum components
Spanco, Inc. warrants its paint and finishes for a period of two (2) years. Warranty claims related to coatings must be accompanied by documentation of the product’s application and environmental conditions from time of delivery to time of claim.
WARRANTY TERMS & CONDITIONS
All warranty claims must be approved by Spanco before any work is performed. Spanco’s obligation under this warranty is limited to the replacement or repair of Spanco products at the factory or separate location approved by Spanco. Other than the above mentioned warranty, Spanco will not honor any other warranties—whether expressed, implied, or statutory—and disclaims any warranties of merchantability or fitness for a particular purpose. Spanco has the right to reject any warranty claim due to harsh and/or inappropriate environmental conditions.
Spanco Is Not Liable for:
- Indirect, incidental, or consequential damages including lost profits, operating costs, loss of production, or travel expenses
- Components or accessories not manufactured by Spanco
- Defective equipment or system failure caused by misuse, negligence, and improper installation or maintenance
- Equipment that has been used in excess of its rated capacity or beyond its service factors
- Equipment that has been altered without Spanco’s written authorization
- Damage incurred by freight carriers
- Any loss, injury, or damage to persons or property resulting from failure or defective operation of material or equipment
Reimbursement Disclaimer:
- Written notice of any claimed system defect must be given to Spanco within ninety (90) days of shipment.
- All requests for reimbursement must be accompanied by proper documentation.
- Reimbursement is provided in the form of a credit unless otherwise approved by Spanco management.
- Reimbursement for labor will be provided at a maximum rate of $75 per hour.
- All reimbursement is subject to approval by Spanco management.
General Design Standards:
Spanco cranes are designed in conformance with the following applicable standards:
- Workstation Bridge Cranes: AISC Steel Construction Manual, OSHA 1910.179, ANSI B30.17, AWS D1.1/D1.6, and MMA MH27.2
- Gantry Cranes: AISC Steel Construction Manual, OSHA 1910.179, ANSI B30.17, AWS D1.1/D1.2/D1.6, and CMAA 74
- Jib Cranes: AISC Steel Construction Manual, OSHA 1910.179, ANSI B30.17, AWS D1.1/D1.6, and CMAA 74
All Spanco cranes have a design factor of 15% of the allowable capacity for the weight of the hoist and 25% for impact.
Fabrication Standards:
All welding performed during the manufacturing of Spanco cranes meets the following American Welding Society’s (AWS) standards: D1.2 for aluminum and D1.1 for steel.
Spanco is officially certified as an AWS Certified Welding Fabricator (CWF). This certification means that not only are all welders AWS Certified, but all processes and procedures adhere to AWS CWF requirements. Examples of requirements include annual calibration of all welding machines and Level 2 visual inspections on all load-bearing components.
Material Standards:
All aluminum used in the manufacturing of Spanco cranes meet ASTM International specification ASTM B308 for 6061-T6 aluminum.
All steel used in the manufacturing of Spanco cranes meets the following applicable ASTM International specifications:
Structural Steel Shapes: ASTM A-36
Structural Steel Pipes: ASTM A-53 Grade B
Structural Square and Rectangular Steel Tubing: ASTM A-500 Grade B
Steel plate and round bar used in Spanco cranes have minimum yield strengths of 36 KSI
Surface Preparation & Painting Procedures:
Spanco adheres to the standards of the Society for Protective Coatings (SSPC) for all product surface preparation. Prior to painting, all Spanco crane components are deburred and descaled using power tools equipped with sanding discs and wire wheels. Components are then washed utilizing a high-pressure/high-temperature biodegradable degreaser solution. Parts are wiped clean and allowed to dry before the painting process. During painting, all components surfaces are coated with a quick drying, semi-gloss enamel, applied to a minimum dry-film thickness of 2 to 3 mils. A finishing coat is applied with a hot, airless, electrostatic spray paint system. Painted components are cured at air temperature.
Deflection Guidelines:
The following guidelines for deflection and stress are followed by Spanco engineers during the crane design process:
- Workstation Bridge Cranes: All models are designed to approximately L/450
- Jib Cranes: Freestanding (100, 101, and 102 Series), Mast Style (200 and 201 Series), Wall-Mounted Cantilever (300 Series), Articulating (400, 401, and 402 Series), and Foundationless models (600 and 605 Series) are designed to approximately L/150; Wall-Mounted Bracket (301 Series) models are designed to approximately L/600 at midspan
- Workstation Jib Cranes: Wall-Mounted (WC Series) models are designed to approximately L/225; Freestanding (FR Series) models are designed to approximately L/150
- Gantry Cranes: All steel series models are designed to approximately L/600; Aluminum models are designed to approximately L/450
Quality Standards:
Spanco is an ISO 9001:2015 Registered corporation. This means that Spanco cranes are manufactured to standards ensuring safety, reliability, and the highest quality. Spanco’s ISO designation also allows for continuous improvement based on customer feedback.
- Inspect entire system annually or more frequently as defined by OSHA 1910.179. Inspection must be performed by a qualified person. Failure to do so may cause serious injury or death.
- This equipment, used as a crane, is not in any way designed for lifting, supporting, or transporting humans. Failure to follow specified load limitations can result in serious bodily injury or death.
- Inspect gantry for missing or broken parts before operating.
- Ensure the rated capacity is clearly labeled on each side of the I-beam.
- Do not lift more than the rated capacity.
- Do not adjust the height or disassemble crane when gantry is under load.
- Do not load gantry on an incline.
- Do not push or pull gantry with a forklift or other vehicle.
- Do not allow the load to swing or roll against support members.
- Do not anchor legs to the floor.
- Do not lift gantry when fully assembled.
- Push the gantry, not the load.
- When moving gantry, keep load as close to the floor as possible and position the load in the center of the I-beam.
- Be certain the load is directly beneath beam before load is lifted. Do not pull sideways on crane.
- Ensure the load is not attached to the floor and remove any obstacles that impede lifting.
- Secure trolley and hoist in the center of I-beam when adjusting height.
- Adjustments and/or repairs should be made in an area where it will have the least interference with operation.
- To prevent the trolley from running off the I-beam, do not use without end stops bolted in place.
- Never stand under gantry when adjusting height or disassembling crane.
- When moving the legs inward, the distance between the A-frames should never be less than the caster frame width and never less than half the total I-beam length.